グローバル・サプライチェーンとは
グローバル・サプライチェーンは、製品の原材料や部品調達から製造・流通・販売に至るサプライチェーン全体を、国内だけではなく海外拠点や調達先も含めて最適化する仕組みと考え方のことである。
サプライチェーンのグローバル化の背景
日本企業のサプライチェーンのグローバル化は、1960年代の高度経済成長期から海外進出が活性化した。1980年代には、製造コスト削減を図るために、人件費や原価が安い中国やアジア圏を中心とした海外への生産拠点シフトが進んだ。
サプライチェーンのグローバル化を加速させた要因の一つとして、通信網やICT技術の進化が挙げられる。計画と進捗状況を見える化し、販売と生産と在庫の各機能を結びつける仕組みが実現できるようになった。また、調達先との連携も可能となった結果、自社グループ内だけでなく、取引先や顧客を巻き込んだEnd to Endでのサプライチェーン改革が進んだ。
グローバル・サプライチェーンのリスク
多くの日本企業で見られるグローバル・サプライチェーンは、特定地域や国に依存していることも多く、国際情勢の不安定化や地政学リスクの影響を受けることが多い。
多国間の通商問題や国際紛争・戦争によって、輸送費や燃料費の高騰、為替相場の急激な変動など、グローバル・サプライチェーンを取り巻く事業環境は大きく変化している。近年発生した新型コロナ危機でのロックダウンの発生に見られるように、グローバル・サプライチェーンが断絶することも世界中で見られた。
こうしたリスクを背景に、グローバル・サプライチェーンをより強靱化し高度化する必要性を認識している日本企業が多くなってきた。
グローバルSCMの必要性
サプライチェーンのグローバル化に伴い、調達・生産・物流・販売の流れやネットワークは世界中に拡大している。結果、リスクが顕在化した場合のサプライチェーンへの影響度合いについて、不確実性が高まっている。
サプライチェーン・マネジメント(SCM)とは
サプライチェーン・マネジメント(SCM:Supply Chain Management)は、原材料・部品の調達、製品の製造から顧客への販売に至る製品供給の業務全体における商流・物流・情報・活動を統合管理する手法のことである。
SCMでは、モノの流れ、情報の流れ、お金の流れと情報を紐づけ、サプライチェーン全体で共有し全体最適を図る。蓄積データなどから需要予測を行い、予測を踏まえた販売計画に対して最適な生産計画を立案する。生産計画に基づき調達管理から生産管理、出荷・配送管理を行うことで、納期遵守で顧客へ届けることができる。
SCMは、グループ企業内だけでなく、仕入先や取引先、協業先との業務・情報連携を行う仕組みを構築することが多い。したがって、業務プロセスの標準化や情報システム連携を行うための統合データ管理が必要となる。また、購買管理や支払管理など、会計システムとの連携なども検討範囲となる。
グローバルSCMが必要な理由
国内のSCMとの違いから、グローバルSCMの要諦とその必要性について整理する。
- 狭い国内、広い海外地域
海外地域は、日本の狭い国土に比べて非常に広い。そのため、必然的にどこで製品を生産し、どのように運ぶかが論点になる。一方で、日本では比較的短時間で届けることができるため、物流や製品供給網に対する重要度が低くなる。
そのため、グローバルSCMでは、生産拠点編成や国際物流網の構築が重要となる。また、物理的に遠隔地になるため、情報システムによるサプライチェーンの見える化が必要となる。
2. 長いリードタイムと膨らむ在庫
グローバル・サプライチェーンでは、海外拠点で生産し製品を運ぶため、国内のサプライチェーンに比べて、リードタイムが長くなる。もちろん現地調達・現地生産にすることで、リードタイムを短縮することは可能であるが、日本国内に比べれば相対的に長い。
リードタイムが長くなると、サプライチェーンの各段階において在庫が必要になる。安全在庫が増加することでキャッシュフローが悪化することになる。こうした経営課題は、国内SCM以上に収益性への影響度が大きく、グローバルSCMに取り組む意義は非常に高い。
3. 多様な不確実性と制約の存在
グローバル・サプライチェーンの起点は、顧客からのオーダー、すなわち需要である。正確な調達計画、生産計画、配送計画を立案し実行するには、需要予測が不可欠になる。
グローバルビジネスにおいては、国内以上に需要予測に基づく販売計画と必要データの供給部門への提供は難しい。需要の変化に合わせて調達計画を変更、更に生産計画を変更する必要があり、多重の変動連鎖が起きる。
では、海外拠点で生産し製品を運ぶため、国内のサプライチェーンに比べて、リードタイムが長くなる。もちろん現地調達・現地生産にすることで、リードタイムを短縮することは可能であるが、日本国内に比べれば相対的に長い。
また、多重の変動連鎖に対応しようとしても、企業の組織能力には制約が存在する。具体的には、原材料や部品の供給能力、工場の生産能力、物流センターからの配送能力などである。いずれも提供能力は無限にはなく、一定の制約があるため、提供可能数には上限がある。
こうした不確実性と制約があるため、グローバルSCMは非常に重要であり、モノとカネと情報を部門横断で一元管理し、最適化することが顧客満足度向上だけでなく収益向上にも貢献することになる。
グローバルSCMのメリット
グローバル・サプライチェーンの不確実性と制約によって、グローバルSCMの必要性が増している。改めてグローバルSCMのメリットを整理する。
顧客への製品供給の安定化
グローバルSCMによって、国内拠点だけでなく海外拠点を含めた調達・生産・配送の一連の製品供給体制とプロセスが統合されるため、顧客からのオーダーに対応した製品提供が可能となる。需要特性を見極め、最適な生産体制と配送体制を構築することで、顧客に対する納品リードタイムを短縮することが可能となる。
生産拠点を複数地域に配置することで製品供給体制のリスクを分散することができる。国際情勢の不安定化に伴うリスク回避手段としても有効である。
在庫削減とコスト削減の実現
需要に応じた在庫の最適管理の仕組みを構築することで、製品の安定供給は可能となる。優れた製品を販売できたとしても、在庫管理が稚拙で製品供給が不安定になると、持続的な収益を確保することができない。グローバルSCMは、国内外における部品調達から販売までモノとカネと情報を統合管理することで、適正在庫とオペレーションの最適化を実現する。
在庫の適正化が実現できないと、収益だけでなくキャッシュフローも悪化するため、業績だけでなく経営の健全性への影響が大きい。
また、グローバルSCMを適切に行うことでコスト削減も実現できる。具体的には、欠品によって販売機会の回避、過剰生産の抑制の両方をコントロールすることができ、販売と供給の両側面から収益性を改善することができる。
グローバルSCMで国をまたがる製品供給体制と業務プロセスの全体を最適化することで、必要な製品を、必要な時に、必要な量だけ供給する仕組みが構築することを目指す。したがって、実際のコスト削減だけでなく、サプライチェーン管理に必要な業務コストの削減も可能となる。
顧客への提案力の拡大
グローバルSCMによる最適な製品供給体制と仕組みの構築により、顧客への提案力が高まる。現地調達、現地生産などの現地化が実現できれば、その対象地域での新しい販売機会を獲得することができる。製品の供給コストも低減でき、収益力も増す。
グローバル調達の体制が構築できれば、顧客ニーズに合致した安く品質の高い部品や原材料を世界中から調達することができる。このようなグローバルSCMの組織能力によって、市場競争における競争優位性を確立することができる。
グローバルSCMの導入方法
グローバルSCMのメリットを享受するための導入手順を解説する。具体的には、生産管理・SCMの教育と認定資格を世界中に普及させている専門団体である米国Supply Chain Council(SCC)が提唱するサプライチェーンプロセスの参照モデルであるSCOR(Supply Chain Operations Reference model)が参考になるので確認して欲しい。
ステップ1:現状実態の評価(SCM成熟度評価)
グローバル・サプライチェーンの現状実態を戦略、オペレーション、プロセスの3つのレベルで整理し評価する。プロセスは6つの組織能力(Capability)で整理し評価すると良い。
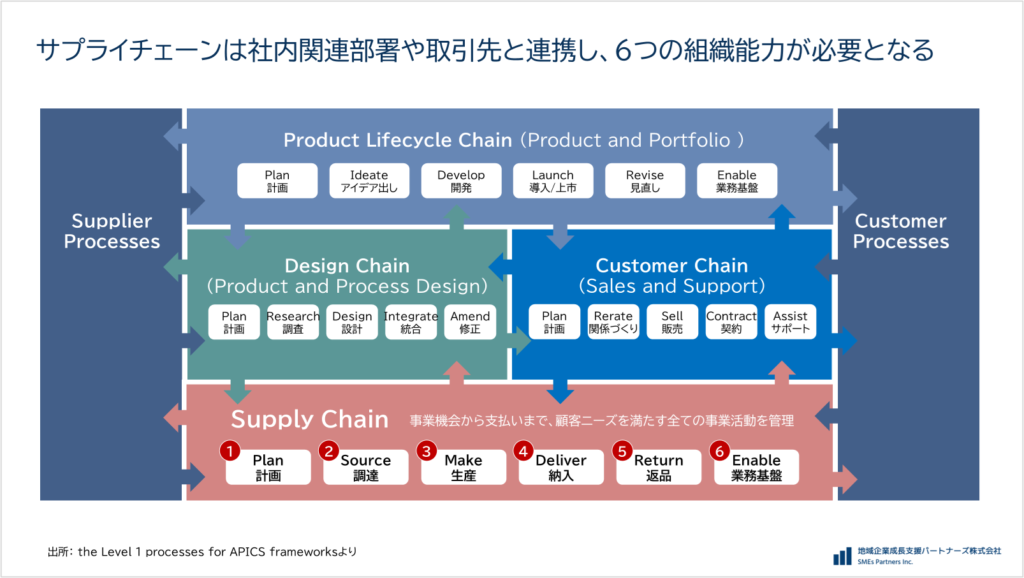
Plan(計画)
サプライチェーンの運営に関する計画プロセス全般が対象である。顧客のニーズ・需要に関する情報収集、製品供給リソースに関する情報収集、需要と供給のバランス、需給ギャップの特定、ギャップ解消策の計画などの実態と評価を行う。
Source(調達)
原材料や部品等の調達に関するプロセス全般が対象である。サプライヤーから納入される商品やサービスの発注・スケジューリング・受入・検品などの業務実態と評価を行う。また、発注書発行、入荷予定管理、材料保管、仕入先からの請求書処理なども含まれる。
Make(生産)
生産に関するプロセス全般が対象である。製造業における材料の加工以外だけでなく、サービスに関わるコンテンツ作成等の活動も含まれる。生産プロセスでは品目番号で情報管理がなされ、入力された材料から異なる加工品や仕掛品の品目番号によって認識される。
Deliver(納入)
納入に関するプロセス全般が対象である。顧客からの受注を起点として、製品やサービスを届ける活動全般の業務実態と評価を行う。具体的には、受注・オーダーの受領、受注内容の確認、出荷指示、配送スケジューリング、ピッキング、梱包、出荷、顧客への請求書発行などが含まれる。
Return(返品)
返品に関するプロセス全般が対象である。具体的には、返品の必要性の確認、対応の決定、返品のスケジューリング、返品物の発送と返却の実態と評価を行う。なお、返品ではなく故障修理や改修、及び再製造のプロセスは、返品プロセスではなく生産プロセスとなる。
Enable(業務基盤)
サプライチェーンの運用に必要な業務及び情報基盤のことであり、情報、リレーション、リソース、資産、ルール・基準、コンプライアンス、契約等の確立・維持・管理に関する活動全般が対象となる。イネーブルプロセスは、サプライチェーンの計画・実行の実現とガバナンスを支援する業務となる。
ステップ2:目指す姿の構想・設計
目指す姿の構想と設計は、サプライチェーン戦略、オペレーション戦略に沿った業務プロセス(Process)を定義するとともに、パフォーマンスを測定する管理指標(Performance)、オペレーションと業務プロセスの実行に必要な人材要件(People)、業務プロセスの遂行方法(Practices)を定義し、設計することが必要である。
なお、測定すべき管理指標は、以下の通り、5つの領域で設定することが望まれる。
- Reliability:信頼性(オーダーの達成率など)
- Responsiveness:応答性(オーダーから納入までのリードタイムなど)
- Agility:機敏性(需要変動への対応力など、例えば増産に必要な時間など)
- Cost:コスト(SCMにかかる費用全般で、材料費、人件費、諸経費など全てを含む)
- Asset Management Efficiency:資産効率(Cash to Cash Cycle-Timeなど)
ステップ3:変革ポイントと変革施策の具体化
変革ポイントと変革施策は、現状評価で整理された現状実態と、目指す姿で構想・設計された状態のギャップを解消するためのポイントと具体策になる。
従って、整理するフレームワークも同様に、戦略、オペレーション、プロセス、管理指標、人材要件、プラクティスでまとめると分かりやすい。
また、成熟度評価で出てきたEnable(業務基盤)、すなわち情報システム基盤についても、変革ポイントと具体的な構築プランを描くことが必要となる。
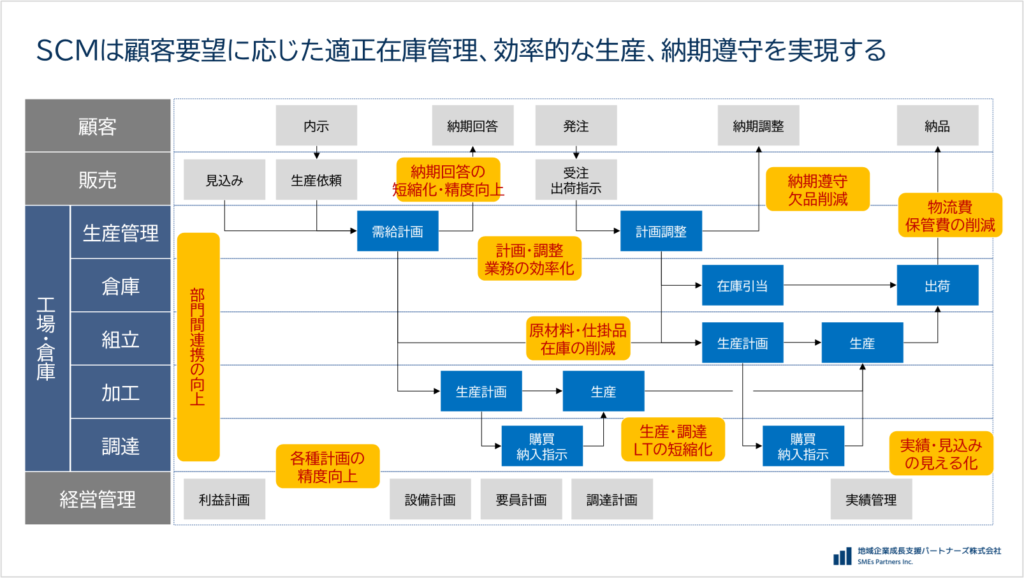
ステップ4:業務プロセス及び情報システムの設計・開発
変革施策の実行計画に基づき、グローバルSCMを実行するためのあるべき業務プロセスと情報システムを計画的に構築することになる。
情報システム設計・開発は、独自システムを開発する場合は、通常の情報システム開発の手順を踏むことが多い(要件定義、システム化計画、要件定義、概要設計、詳細設計、開発、テスト、導入教育、導入)。パッケージソフトを利用する場合は、要件確認、製造パターン別プロトタイピング、マスタ検証、実データ検証、運用確認、並行稼働という流れになる。
ステップ5:SCM導入と定着
導入時は、新しい情報システムの操作教育と運用教育が必要となる。業務が止まらないように並行稼働も検討される。初期流動期には、問合せ対応を含むPMO(Project Management Office)を立上げ、変革管理を徹底することが重要となる。
営業や生産や開発などの基幹業務との連携が必要であるため、情報システム担当だけでなく、業務やマネジメントに対する理解がある人材がPMOに配置することが必要となる。
グローバルSCMの事例
経済産業省のグローバル・サプライチェーン高度化研究会の報告においては、デジタル時代におけるサプライチェーンデータの共有ニーズが大きく4つの領域で存在すると整理している。効率化の観点だけでなく、強靭化、設計連携、サステナビリティのテーマでまとめられている。
デジタル時代のサプライチェーンデータ共有のニーズ
1.サプライチェーンの効率化
テーマ | 取組み事例 |
サプライチェーン計画 | 顧客需要と連携した自社生産計画・キャパ調整 |
モノの流れ | 在庫(部品・完成品) の可視化・共有輸送状況(物流・港湾) の可視化・共有 |
カネの流れ | 受発注データの可視化・共有 |
キャパシティ | ヒト・設備の稼働状況の可視化・共有 |
2.サプライチェーンの強靭化
テーマ | 取組み事例 |
サプライチェーン構造 | サプライヤツリーの可視化・共有販売・倉庫ネットワークの可視化・共有 |
リスク予兆 | サプライヤリスクの可視化・共有マクロ・リスク指標の分析・アラート |
サプライチェーンの パフォーマンス・断絶状況 | 設備稼働・スループットの可視化・共有フリート・ロジスティックスの可視化・共有 |
3.エンジニアリングチェーンの連携
テーマ | 取組み事例 |
設計・R&Dデータ | Addictive製造(3D造形) のデータ共有R&D・設計関連データの共有 |
工場・ライン情報 | 設計・製造ライン情報の共有デジタルツイン・バーチャルファクトリー |
4.サプライチェーンの強靭化
テーマ | 取組み事例 |
規制対応状況 | カーボンフットプリントの可視化・共有人権・品質トレーサビリティの可視化・共有環境規制の対応状況の可視化・共有 |
事例1:株式会社ダイセル ダイセル式生産革新
出所:経済産業省「製造業DX取組事例集」
背景・課題
- 各工場は歴史的な出自が異なっており、各々で生産性向上等に取り組んでいたが、個別最適化されていたことから、グループ全体のシナジーが生まれていなかった。
- 各工場内においても、工程が分断されて個別最適化されており、工場全体の製造プロセスを最適化する視点が欠けていた。
- プロセス型産業であるにも関わらず人が介在する業務が多数あったことから、設備や材料起因の工程不具合を直す等、あるべき姿から離れた状態を人が正しているのではないかという考えに至った。
取組み内容
- 共通の切り口で現行業務の在り方を点検の上、全体像を把握してマスタープランを策定。
- 業務のムダやロスを排除し、製造担当者の負荷軽減・安定化と言語や図面の統一を実施。
- 製造担当者の意思決定プロセスの標準化手法として、オペレーションを「安全」「量」「品質」「コスト」の要素ごとに監視→判断→操作の流れで明らかにし、原理原則と照らし合わせて現場ノウハウを検証し、裏付けが取れたものをデータベースとして整理する「総合オペラビリティスタディ」を実施。
- 後戻りしない仕組みとして、データベースをシステム化。
成果
- 製造プロセスにおける品質向上、安全性強化、コスト削減、標準化を確立し、「ダイセル式生産革新」として仕組み化した。
- 他の製造業企業へのライセンス供与を行い、広く普及・活用されるようになった。
- 製造プロセスを確立したことで、要求品質の高いグローバル企業等、新規顧客の開拓につながった。
- 「生産革新(プロダクションイノベーション)」で固定費を削減、「プロセスイノベーション」で変動費を削減、その後「プロダクトイノベーション」で利益を創出、というステップで経営戦略を立てることで、製品競争力を維持する原動力になっている。
事例2:ヤマハ発動機株式会社 経営目線のデジタル改革実行
出所:経済産業省「製造業DX取組事例集」
背景・課題
- 従来、問題点の改善を地道に行い売上拡大を目指すアプローチを続けていたが、経営目線の戦略的アプローチが欠けていた。
- エンジニアリングチェーン・サプライチェーンそれぞれを担う製造システム・基幹システムやツール類をIT子会社で長年内製してきたが、工場や支店の海外展開が拡大する中、それぞれの拠点においても独自システムが作られるなど個別最適化されており、非効率なやり取りがなされていた。
- 自社商品に対するニーズの把握やターゲットに合わせた商品の展開が不足しており、「消費者にとって価値のあるものづくり」から離れてしまっていた。
取組み内容
- 戦略的アプローチによる売上拡大や予知型経営の実現を目指すため、合宿や1on1ミーティングにより経営陣の意識改革を実施し、トップダウンでグローバル事業所全体に向けて発信した。
- 「既存のビジネスの効率化」「未来のビジネスの創出」を目的とし、マーケティングや生産部門など様々なバックグラウンドの人材を集め「デジタル戦略部」を立ち上げた。
- 「デジタルマーケティング」「コネクテッド」「スマートファクトリー」「データ分析」の4つのテーマで年間数十個のPoCによる検証を実施、センサーによる生産データ収集と分析、ナレッジのデータ化等を行った。
- 各拠点でばらばらだった基幹システムについてさらに、外部パートナーと連携し、どのようなデータをどこでどのように収集・階層化し、どう活用するのかといったデータのライフサイクルマネジメントについての検討も行っている。
成果
- デジタルツールの導入により、エンジニアリングチェーンの省人化、効率化を実施した。
- 新設組織にてデジタル技術を使ったPoCを年間数十個実施し、不良率低減等の効果を上げた。
事例3:オムロン株式会社 i-BELT
出所:経済産業省「製造業DX取組事例集」
背景・課題
- オムロンにおけるエンジニアリングチェーンでは、日本で開発・設計した後、工程設計以降をグローバルで行うことがあるため、データというよりも運用の確立、ものづくりや設計思想のカルチャーの融合が重要で、その後、標準化に向けたデータの流れを考える必要があった。
- 日本企業のデジタル化を阻む要因として、日本企業のヒエラルキー的な特徴による現場と各部署との断絶や、分業化による総合的な知識・技術を兼ね備えた人材の不足、社内外とのコミュニケーション・情報連携不足、対グローバルでの競争力の低下などが挙げられる。
- デジタル化の恩恵を受けるうえで肝となる、データの現状把握→可視化→課題・ゴール設定→業務設計という仕組みを構築できる企業、またはそういった事が分かる人材がいる企業が、日本に少なくなってきている。
取組み内容
現場データ活用サービスである「i-BELT」を、「生産管理」「品質管理」「設備効率」「エネルギー」の4つの切り口で展開し、ツールだけでなく、トップダウン(経営指標、取組む目的)とボトムアップ(目標の共有、効果の見える化と実感)の連携強化プロセスの支援サービスを、以下のステップで顧客へ提供している。
① 顧客企業内部の様々な技術や知見の棚卸して現状把握をし、何をデジタル化することが最も有意義なのかを見極める。
② データの流れやプロセスを可視化し、構造化をする。
③ 顧客の既存の資産(データ・設備)を活用して価値が最大化できる部分に対して、データ化や最適化を提案する。
成果
- 「i-BELT」の活用により、製造現場において作業効率の安定化、工具の摩耗量の削減、加工時間の削減などを実現した。
- 「i-BELT」の他社への展開により、暗黙知の形式化と現場モチベーションを向上させることで日本企業のデジタル化の推進に貢献した。
3つの事例のまとめ
各社では、基本的にグローバルSCM導入の5ステップを現状実態評価から行っている。課題の共通点は、個別最適の運用からの脱却と部門間コミュニケーションの活性化・仕組みづくりである。
顧客起点でサプライチェーンの現状実態を見える化することから取組んでおり、実態把握と目指す姿を描くことが変革の要諦と言える。